Home ⇒ Overview Courses ⇒ Electric drives ⇒ Motor protection
Motor Protection
There are basically two ways to protect an electric motor from overload during operation:
- Monitoring of its power consumption e.g. by Motor protection switch or Motor Protection Relays
- Direct monitoring of the temperature of the motor winding e.g. by thermistors, which is also known as full motor protection.
Motor protection switch or Motor protection circuit breaker MPCB
The motor protection switch, also known as Motor Protection Circuit Breaker MPCB basically serves as overload protection, not-self starting (which means a very high current for induction motors) and failure of an external conductor of a 3-phase motor.
Two releases are installed: a thermal release using a bi-metal, which must be adjusted to the rated motor current, and an electromagnetic release, which provides short-circuit protection.
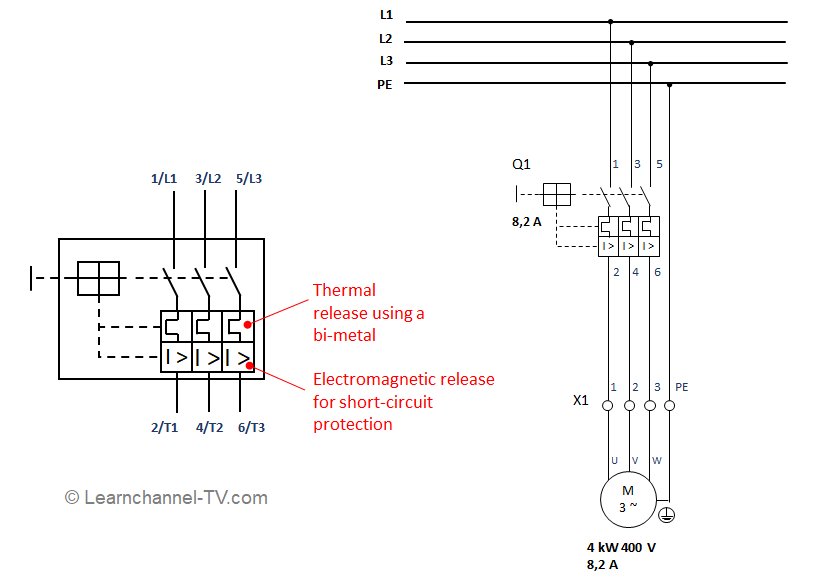
Motor protection switch - Symbol, function
Motor protection relay or overload relay
With the motor protection relay or overcurrent relay (overload relay) the switch-off is only thermal and via control contacts, that means a contactor must be used as switching stage.
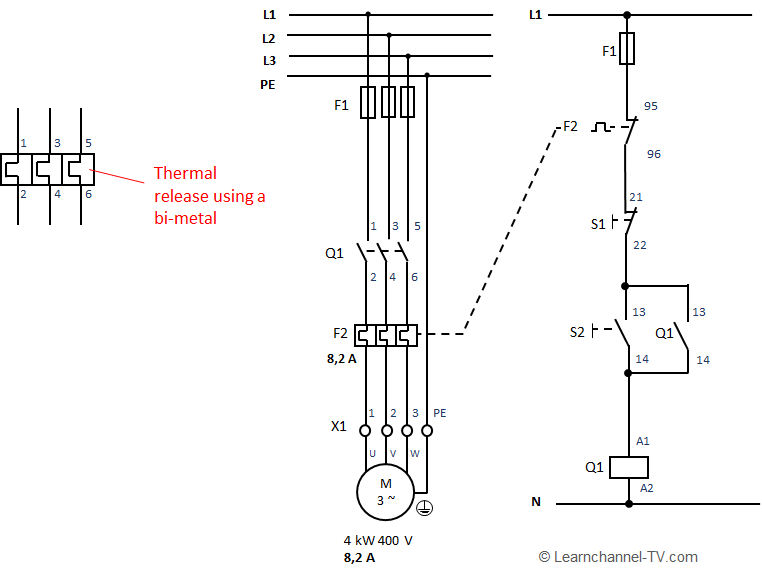
Motor protection relay
Motor Thermal Protection
Problem: The motor winding can overheat even if the rated current is not exceeded. Reasons for this can be: Ventilation slits are dirty, ambient temperature too high. The motor protection switch would not respond here.
Solution: The temperature of the motor winding is measured directly by a thermistor (PTC thermistor).
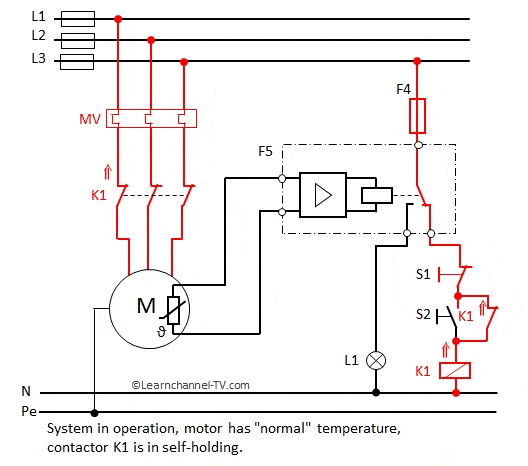
Thermal Motor protection with thermistor - How it works and circuit example
Note: Since the temperature of the motor winding is detected directly, the full motor protection is suitable for all types of electric motors, independent of the current and connection type.